Transformadores de Potencia
Transformadores de Potencia
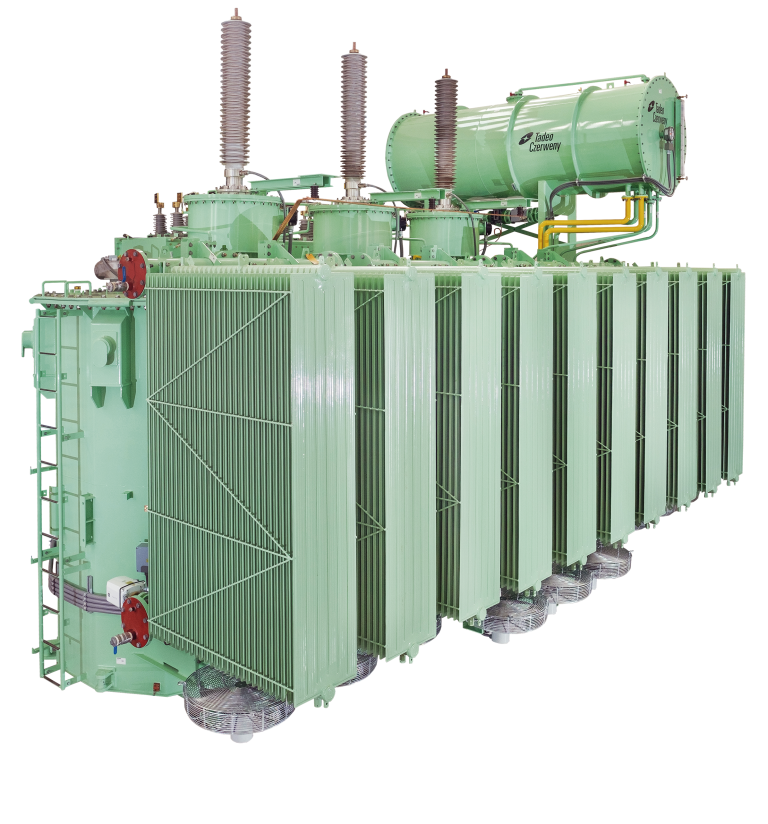
Prestigio y Confiabilidad
Tadeo Czerweny S.A. produce transformadores de potencia y media potencia en una gama que va de 5 a 100 MVA. y con tensiones de hasta 230 KV.
Estos transformadores se fabrican con conmutadores sin tensión y/o automáticos bajo carga, de acuerdo a los requerimientos del servicio a los que serán destinados, siguiendo los lineamientos de las Normas IEC, ANSI, IRAM, ABNT o Normas particulares de los Usuarios.
Tadeo Czerweny S.A. también ofrece soluciones específicas para requerimientos especiales y particulares, satisfaciendo todos los requisitos relacionados a cada tipo de operación, como ser, bajo nivel de ruido, bajas pérdidas, cubrebornes en baja y media tensión, bridas en alta tensión para acople de ductos en SF6, arquitecturas especiales, como así también servicios de transporte, instalación, supervisión y/o puesta en servicio de sus transformadores.
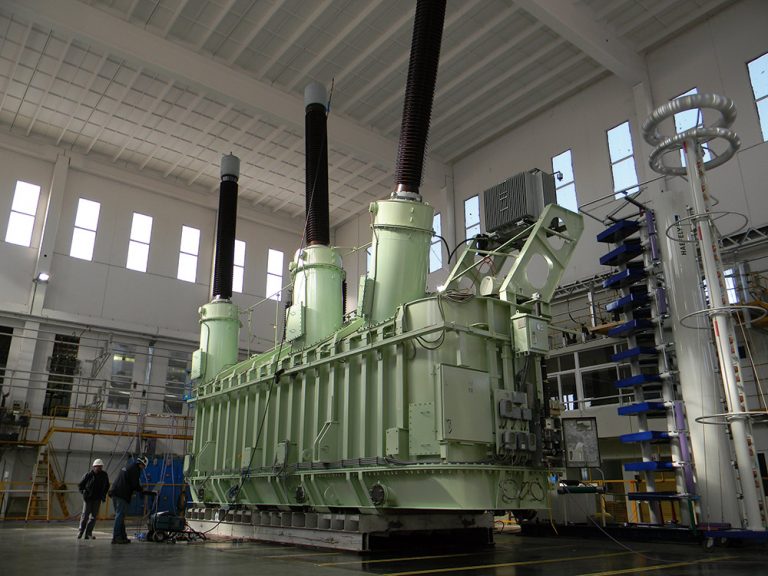
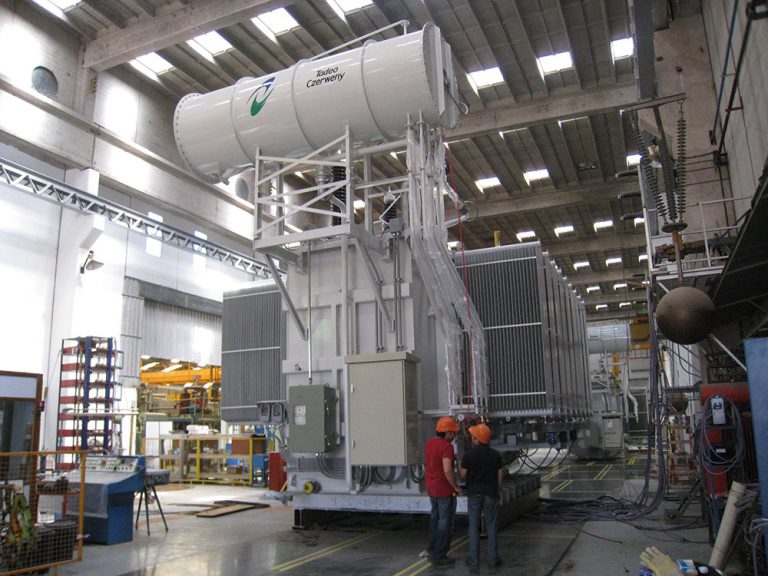
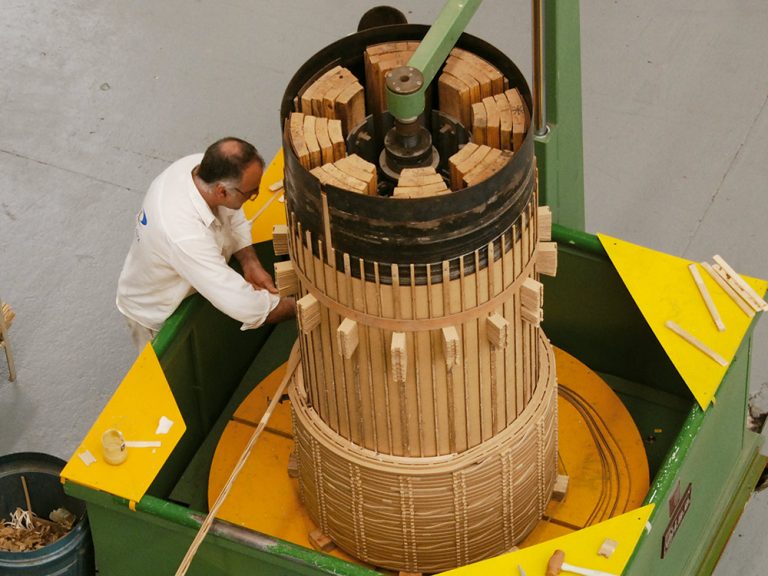
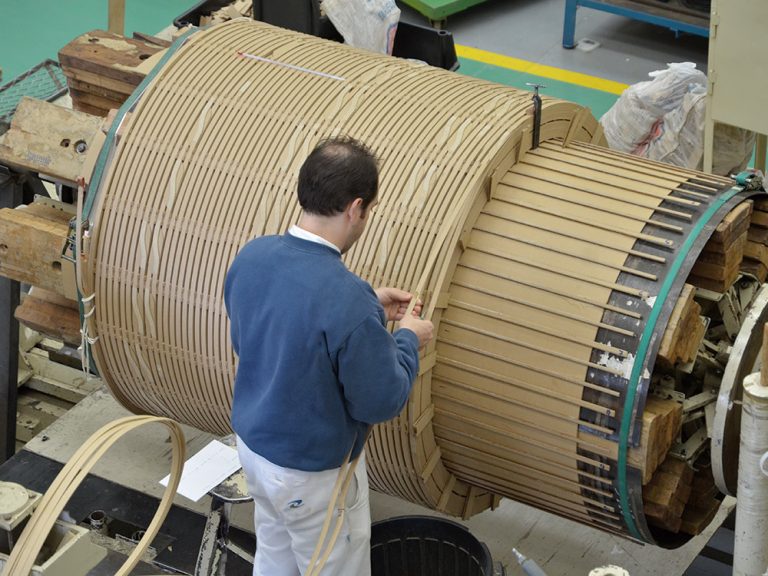
Generalidades constructivas
APLICACIONES
- Generación, Transmisión y Distribución de energía.
- Industrias
- Infraestructura
- Energías renovables
- Especiales
- Grandes consumidores